How should I start my Predictive Maintenance Program?
Which machines should I measure and when?
You need to consider which machines are critical for your factory’s production. These critical machines should have the biggest priority over the other machinery and you should also consider how much time you can spend to measure them regularly. It is ideal to measure the machines every week, but we are not living in an ideal world. Despite that, try to schedule measurement of those particular machines at least once per month.
Note: If you plan to measure your machinery every half a year, please close this document and throw your vibration meter / analyzer into the trash. It does not make any sense to measure with such a huge time span. It would not be predictive maintenance but the run to failure method. Imagine how many things can happen during this half a year…
The basic vibration meter with accessories
Let’s explain what the basic vibration measuring equipment looks like. It consists of the following parts:
- Vibration meter (analyzer)
- Cable
- Vibration sensor (acceleration sensor)
How does it work? You place the vibration sensor on the (vibrating) measuring point, the vibrations are changed to electronic signals (voltage) in the acceleration sensor, the signal is transmitted by the cable to the vibration meter (analyzer) and the signal in the meter (analyzer) is processed to the vibration values which you can read from the vibration meter screen.
Measurement Point
The measurement point is the place on the machine (usually a bearing housing) where you will be placing a vibration sensor and where you will be taking your vibration reading (measurement). The measurement point location must enable you to take repeatable measurements under the same conditions every time. Measurement repeatability is very important!
How should I prepare my measuring point?
To obtain quality and repeatable measurements you should prepare your measuring point on the bearing housing. The best way to do that is to fit all measurement points with measurement pads. A measurement pad has flat ground surface, made of magnetic stainless steel and it is connected to the machine with a special glue (with metallic properties when dry) which ensures good vibration transmission. An acceleration sensor is usually supplied with a strong magnetic base (neodymium type) which ensures good transfer of machine vibrations to the sensor.
Measurement pad - ideal solution
- Measurement pad (glued on the motor)
- Magnetic base
- Acceleration sensor
Measuring pad - ideal solution
Avoid placing the sensor just on the bearing housing. The flat magnetic base will be swinging on the rounded bearing house and such a measurement is useless.
Wrong placing of sensor
If you don’t want to glue measurement pads on your bearing housings then you can use a magnetic base for curved surfaces. There is a disadvantage, that such a magnetic base has a little bit worse transmission of high frequency vibrations (bearing vibrations).
Magnetic base for curved surfaces
Do not measure on motor fan covers. Fan covers are weak and they don’t transmit the “real” vibrations of the machine. Bearing vibrations are not there at all.
Do not measure on motor fan covers
Do not measure on rusty or painted (or both) bearing housings. Rust and paint significantly damps high frequency vibration transmission (bearing vibrations).
Do not measure on rusty or painted surfaces
Directions and locations of measurement points
The direction of the measurement point (radial and axial according to shaft rotation) is important as well. Again, in ideal world you would measure in a vertical-radial direction and a horizontal-radial direction on each part of the machine. But then you will spend twice as much time on each machine to collect the data.
Let’s make a compromise. Place the measurement point (sensor) at 45 degrees (if possible) in a radial position. You will still have information about both (vertical+horizontal) directions and you will spend less time on the machine.
You should also measure one axial point. Don’t measure the axial direction on the motor non drive end but measure it for example near some joints of individual components (for example near couplings).
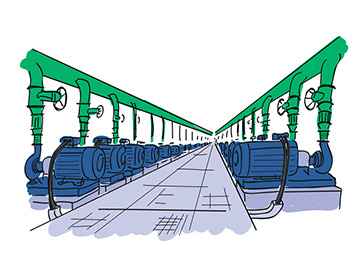